Blog
Choosing the Right Spinning System: Why LMW is the One-Stop Smart Solution
In today’s highly competitive textile industry, selecting the right spinning system is crucial to achieving high productivity, consistent yarn quality, and maximum return on investment. From fiber preparation to yarn winding, every stage must operate in harmony. This is where LMW stands apart — as a complete spinning system provider offering cutting-edge machinery, integrated solutions, and unmatched technical support under one trusted brand.
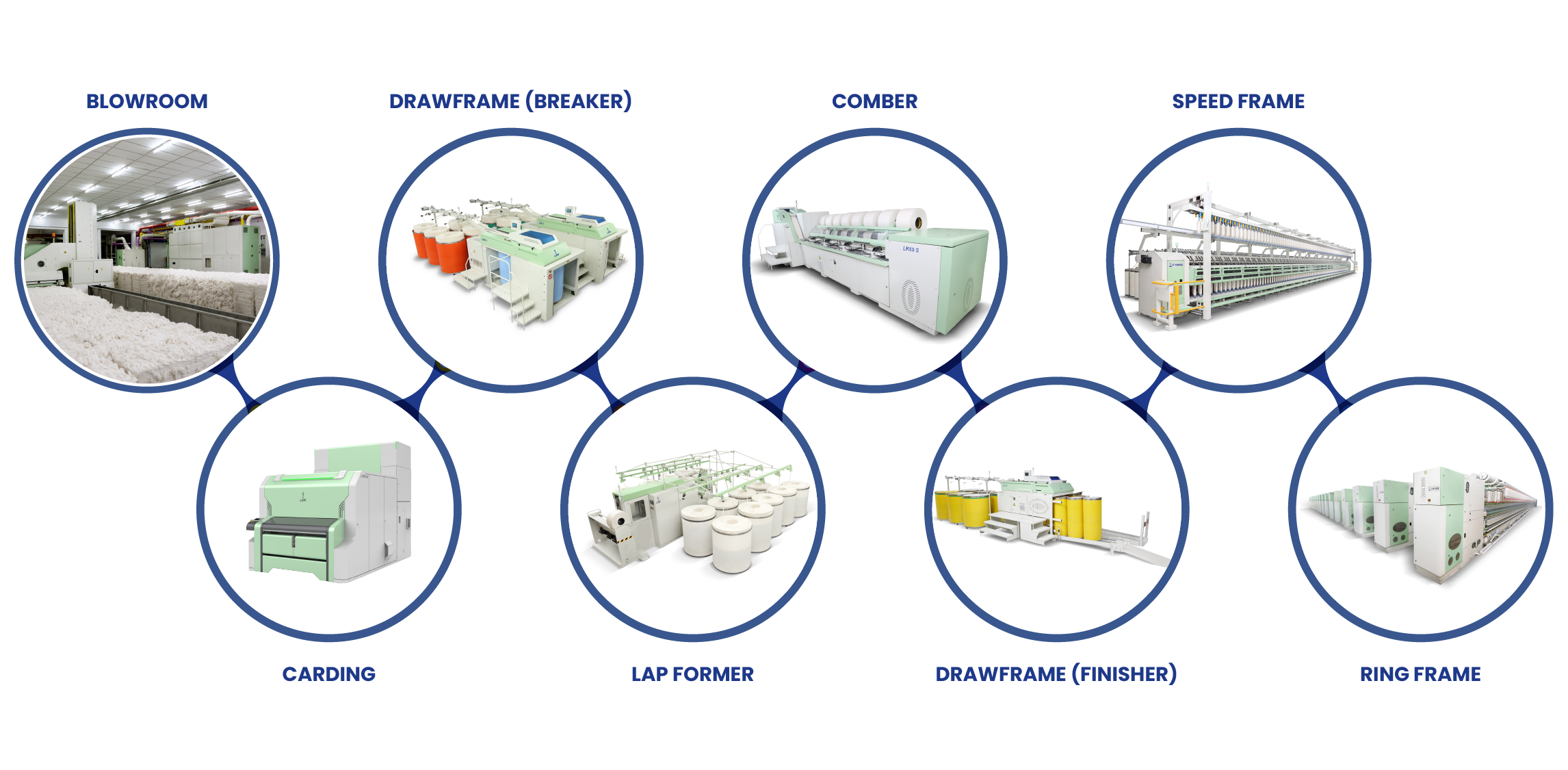
LMW’s Textile Machinery Division (TMD) offers a full spectrum of spinning machinery, engineered for seamless process, resulting in uninterrupted production flow and simplified maintenance.
Key Steps in the Spinning Process
Blowroom:
The Blowroom process begins by opening the material into very fine tufts,
preparing it for further cleaning and processing. Cleaning eliminates most
impurities, such as seed particles and debris, ensuring cleaner fibers.
In mixing or blending two or more types of fibers are blended to achieve
a uniform and consistent mix. LMW's versatile GENTLE BLOWROOM LINE is
designed to process cotton, manmade, and regenerated fibers, making it
ideal for all spinning applications.
Bale plucker LA23/S, automated line with production capacity of up to 2000 kg/hr with auto scanning arrangement and suitable to process 4 assortments.
Swift floc LA21, automated line with production capacity of up to 600 kg/hr, suitable to process 2 assortments.
Varioclean LB9/2, Integrated opening, cleaning and dedusting machine with a production capacity of up to 1600 kg/hr.
Unimix LB 7/4 and LB 7/6, High output of up to 800 kg/hr with 6 Chambers (LB7/4) and 1000 kg/hr with 8 Chambers (LB7/6). Enhanced value of mixing through homogeneous blending and efficient opening and cleaning with automatic grid bar to beater setting.
Flexiclean LB5/6, Controlled fibre feed for optimum opening and maximum cleaning efficiency with a production rate of up to 600 kg/hr with working width of 1200mm.
Supremoclean LB10/2, the machine is equipped with a pressurized feed chamber for material feeding, uniform filling by feeding flaps and trio feed roller for better compacting. The production capacity is up to 1000 kg/hr.
Auto blend LA10, blending of various material with a maximum throughput of up to 2000 kg/hr (4 modules with max. 500 kg/hr each). Automatic feeding system without any Manual Intervention to blending accuracy levels of +/- 1%. Minimum blending ratio possible is 99:1.
The Gentle Blowroom Line includes the following machines:
Card:
Carding machines align the fibers into thin webs, separating
and cleaning them further. This step individualizes the fibers and
converts them into a strand called the sliver.
The LMW Card LC363 / LC361 is designed for high production—up to 150 kg/hr—with advanced features that ensure high-quality sliver across all varieties of cotton, man-made fibres, and blends. Card LC363 / LC361 is configured to produce better yarn characteristic with reduction in running cost.
With LMW’s Card LC636 SX wider width card (1.5m) is engineered to boost both productivity and quality, making it ideal for modern spinning mills. It empowers mills to achieve superior yarn quality while significantly improving overall operational efficiency.
Draw Frame (Breaker):
In the Draw Frame process, the carded
sliver is further refined to enhance its uniformity. This is
achieved by improving its evenness across short, medium, and long
lengths. The fibers are parallelized through drafting, ensuring they
align uniformly within the strand.
LMW’s LDB3 redefines the way Non-Auto leveller draw frames perform in spinning preparatory. It comes in two variants: Electronic drafting drive and Mechanical drafting drive. With unique feature of in-built closed loop digital sliver control system, LDB3 ensures highest degree of consistency in linear density of delivered sliver.
Lap Former:
Experience unmatched efficiency and quality with LMW’s
Lap Former LH20 S, meticulously engineered for seamless integration
with the LK69 Comber Series. Capable of delivering speeds up to
200 mpm and producing up to 680 kg/hr, this powerhouse boosts
productivity while minimizing operational costs.
Comber:
The Comber process focuses on enhancing the quality of the
fiber by removing short fibers and any remaining impurities from
the material. This step ensures that only long and consistent
fibers remain, resulting in improved yarn strength and quality.
The fibers are then consolidated into a highly uniform strand
called a combed sliver. Starting with the comber lap as input,
this process produces a combed sliver that is highly refined
and ready for further stages of spinning. LMW’s latest Comber
LK69 S, represents cutting edge technology engineered to
deliver exceptional productivity and better fiber quality.
LMW Draw Frame (Finisher):
A Drawframe Finisher is a crucial machine in the
spinning process used to improve the sliver quality by doubling and
drafting the carded or comber slivers. It aligns the fibers parallel,
equalizes the sliver weight, and enhances fiber blending to ensure
uniformity and consistency in the yarn quality.
LMW’s Autoleveller Draw Frame LDF3 S is equipped with best in class in features like Servo draft, change gearless main motor, Auto piecing along with online sliver monitoring. Since LDF3 S delivers benchmark quality at affordable price, it became instant success among customers.
LMW’s Twin Delivery Auto Leveller Draw Frame – LDF3 2S, a revolutionary solution designed to elevate spinning efficiency and sliver quality. With its innovative compact design, the LDF3 2S maximizes space utilization while delivering high performance.
Speed Frame:
The Speed Frame process takes the drawn sliver
to achieve the desired thickness. A small amount of twist is
introduced to hold the fibers together, forming what is
known as roving—a pre-yarn intermediate state. The twisted
roving strand is then wound onto bobbins, making it convenient
for handling and transportation to the next stage. This stage
transforms drawn sliver into roving, a crucial step toward creating
high-quality yarn. LMW offers model with Auto doffer is the most
advanced Speed Frame available in the market that provides highest value to the customer.
Ring Frame:
The Ring Frame process is where the roving is transformed into yarn.
This begins with drafting, where the roving is drawn to a specific degree of
fineness. The fibers are then twisted, creating a continuous and durable
strand of yarn. LMW’s LRJ 9/SXL Ring Frame enhances productivity, efficiency
and quality in the spinning industry. With cutting edge technology and advanced
features, it offers energy-saving, reduced footprint, high user and maintenance
friendliness. A game-changer to elevate your spinning process.
LMW’s RAP is a state-of-the-art automation solution designed to reduce manpower by up to 50%, significantly enhancing operational efficiency. With a shorter auto piecing cycle time and a piecing rate of up to 60/hour, it ensures seamless and precise piecing for improved yarn quality. The system maximizes productivity, achieving an efficiency of over 85%, making it a highly reliable automation tool for modern spinning operations.
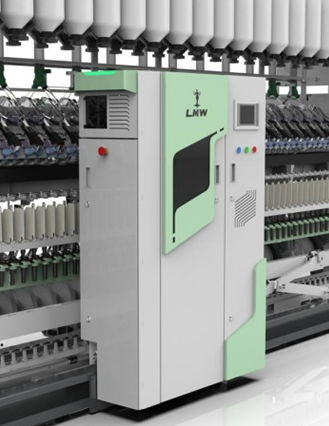
Mill Network System – LMW's Spinconnect is a web-based monitoring and control application that seamlessly networks the entire spinning process—from Blow Room to Winder. The system captures and displays key parameters such as speeds, production, stoppages, quality, power consumption, and more, enabling close monitoring of plant utilization and productivity levels.
Why LMW is the Ultimate Choice for Spinners
- High-quality outputs with reduced manpower and energy costs.
- Smart technology at every stage.
- Robust after-sales service and original spare parts.
LMW RESPIN Impact
As the textile industry moves towards a more sustainable future, circularity has become a key focus. With the growing global demand for eco-friendly practices, LMW is at the forefront of this transformation, offering innovative solutions for recycled fiber processing. LMW RESPIN is a commitment to a sustainable future. It is designed to integrate sustainability, innovation, and performance, enabling textile manufacturers to adopt eco friendly practices. Various raw materials / feed materials are used in the recycled process. Virgin material of cotton and polyester are added as per the end product requirements.
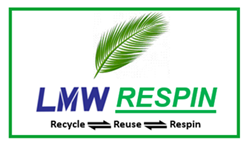
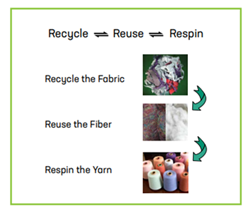
Conclusion: Future-Ready Spinning Starts with LMW
Whether you are setting up a spinning unit or upgrading existing operations, LMW offers a holistic solution that minimizes risk and maximizes ROI. By choosing LMW, you’re not just investing in machines — you’re investing in a strategic partner committed to your success.