Blog
Inside the Mill with LMW: Smart Maintenance at Every Stage
Introduction
In the high-speed world of textile spinning, every minute of machine downtime equals lost productivity. While many mills focus heavily on production and quality, one often underestimated pillar of performance is maintenance. Regular, well-structured maintenance isn’t just about keeping machines running—it’s about maximizing machine life, reducing operational costs, and ensuring consistent yarn quality.
The three pillars of smart maintenance—Preventive, Predictive, and Breakdown Maintenance—play a crucial role in ensuring reliability, productivity, and machine longevity.
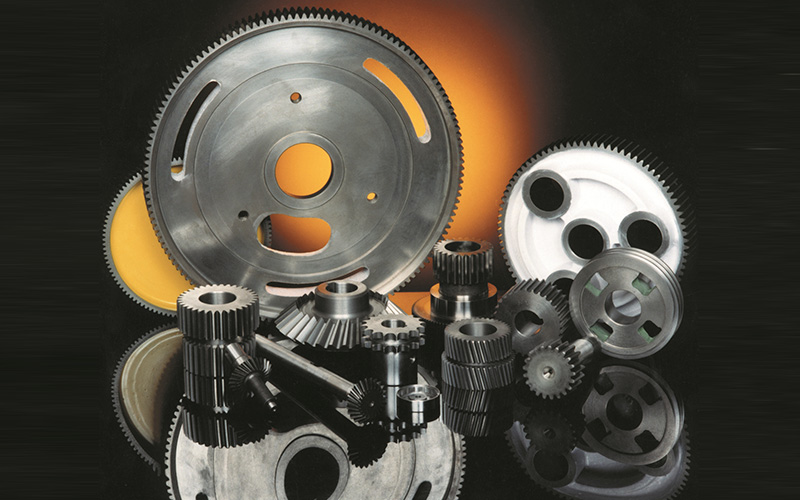
Preventive Maintenance
Preventive maintenance is scheduled and systematic servicing of machines to reduce the likelihood of failures and ensure smooth operation. It is based on time intervals or machine usage hours.
Key Actions
- Lubrication and greasing of moving parts
- Inspection and replacement of worn-out components
- Tightening of belts, chains, and couplings
- Cleaning filters, sensors, ducts, and panels
- Checking alignment and tension of drives
Benefits
- Minimizes unplanned downtime
- Increases machine lifespan
- Improves production consistency
Predictive Maintenance
Predictive maintenance uses real-time data and monitoring tools to predict when a machine or component is likely to fail. This enables maintenance only when necessary, reducing costs and avoiding unnecessary interventions.
Key Tools & Practices
- Vibration analysis to monitor bearing health
- Tomography to detect overheating components
- Condition monitoring via sensors in smart machines
- IoT-enabled machines
Benefits
- Maximizes up time
- Optimizes maintenance scheduling
- Reduces spare parts inventory costs
Breakdown Maintenance
Breakdown maintenance is reactive and performed after a failure occurs. Though not ideal, it's unavoidable in certain scenarios.
Common Causes
- Electrical faults (motor burnout, control panel issues)
- Mechanical failure (gear wear, shaft misalignment)
- Lack of preventive care
Minimizing Impact
- Maintain critical spare parts
- Train operators to detect early warning signs
- Use modular designs for quicker replacements
LMW’s Maintenance Support
LMW has been at the forefront of enabling this transformation. Its machines are not only built for performance but also designed for maintenance-friendly operation.
To further this commitment, LMW operates service stations at Coimbatore and Indore, bringing expert care and original service closer to our customers.
LMW’s Service Station continues to strengthen our commitment to customer support with:
- Advanced test jigs and genuine parts for repairs
- Skilled manpower to ensure high-quality servicing
- Comprehensive facilities for all LMW products
Beyond repairs, our service support extends to specialized audits, helping mills achieve sustained performance improvements.
Service Focus Areas
- Machinery Health Audit
- Value Added Services
- Maintenance Audit
- Quality Audit
- Productivity Audit
LMW has been at the forefront of enabling this transformation. Its machines are not only built for performance but also designed for maintenance-friendly operation. From fibre opening to yarn winding, LMW offers a complete suite of smart spinning machinery.
Key Steps in the Spinning Process
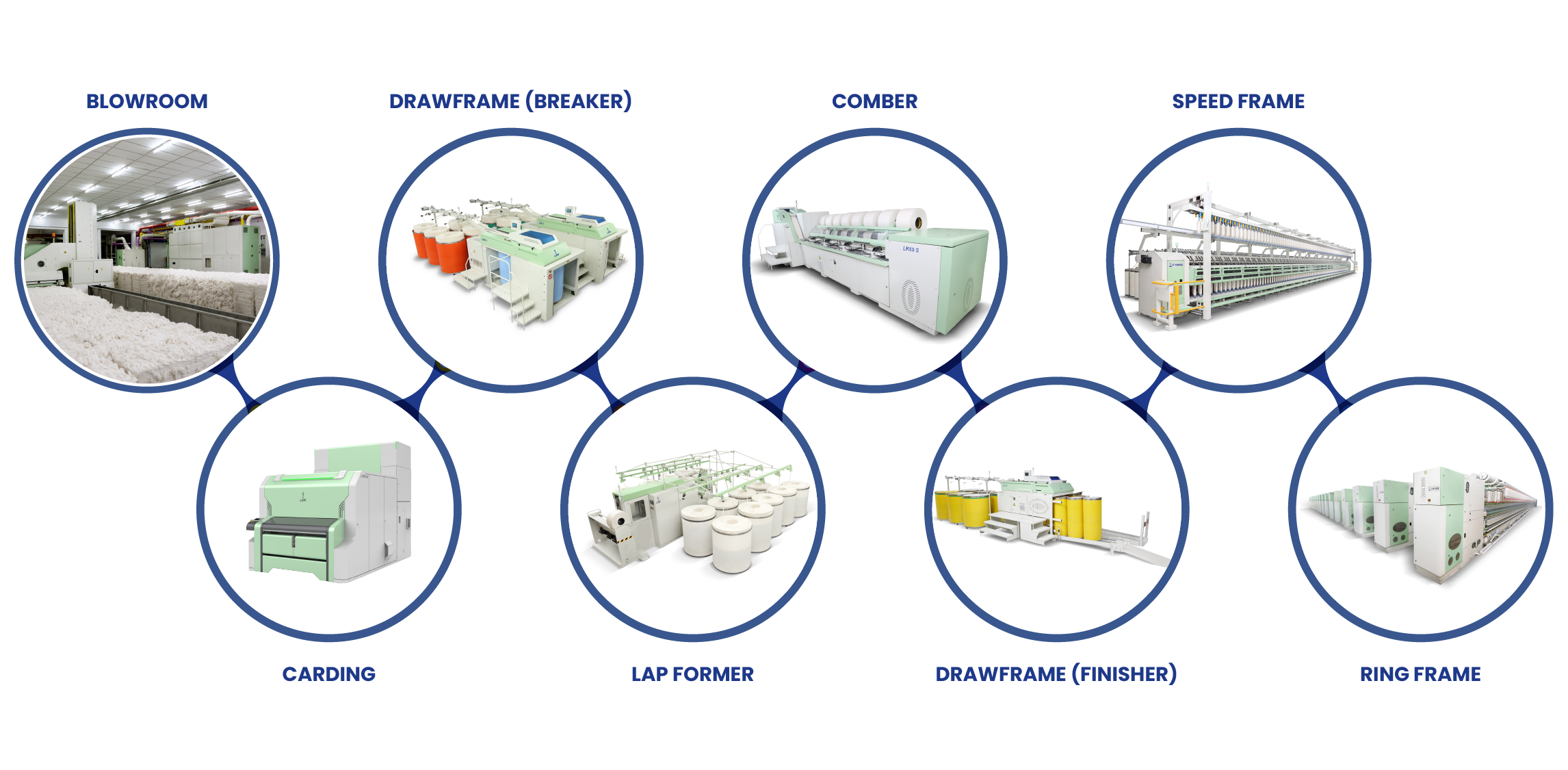
Machine-wise Maintenance Practices in Spinning Mills
In a spinning mill, each machine in the process line requires a tailored maintenance approach to ensure peak efficiency and longevity.
Blowroom
Starting with the Blowroom, regular preventive actions include cleaning of sensors, ducts, and filters, along with proper lubrication of beaters and chute mechanisms. It’s essential to ensure the alignment of feed rollers and conduct periodic inspection of fans to maintain consistent airflow and fiber movement.
Predictive maintenance techniques may involve monitoring motor temperature, airflow pressure, and using alert systems for dust accumulation. Common breakdown issues like belt slippage or motor overload often arise due to blockages or poor airflow, making timely diagnostics critical.
To support uninterrupted operations, LMW offers a comprehensive range of Blow room service components, including:
- Disc Beater, Saw tooth Beater – optimized for efficient fiber opening
- Lattice Assembly – for smooth and uniform material conveyance
Carding
Moving to the Carding, maintaining wire integrity on the flats, cylinder, and doffer is critical for ensuring consistent fiber opening and transfer. Regular tasks include inspecting wire wear, maintaining correct gauge settings, and cleaning suction areas to prevent fiber build-up. Additionally, bearings and chains require periodic lubrication to reduce friction and wear.
Predictive maintenance tools help monitor motor load patterns, suction efficiency, and the effectiveness of automatic flat cleaning systems. These insights help mills pre-empt issues like wire damage from metallic contaminants or licker-in clogging, which can lead to uneven carding or machine downtime.
To support performance and durability, LMW offers essential carding service components, including:
- Full Width Grinding Roller Assemblies – to maintain optimal wire sharpness and surface profile
- LC300 V3 & V4 Coiler Units – for reliable web delivery and precise sliver coiling
Draw Frame
The Draw Frame—across both Breaker and Finisher stages—plays a vital role in maintaining sliver quality and drafting precision. To ensure consistent performance, preventive maintenance focuses on greasing rollers and bearings, calibrating auto-levelers, cleaning the drafting zone, and regularly checking belt tension. In the Finisher stage, where tighter tolerances are essential, special attention is given to roller apron inspection and fine-tuning of drafting elements.
Predictive maintenance strategies leverage real-time sliver variation systems, roller pressure monitoring, motor load tracking, and gear vibration analysis—all of which help in identifying early signs of component fatigue, misalignment, or overload conditions. Ignoring these indicators can lead to breakdowns stemming from worn aprons, gear failures, or auto-leveler issues, directly impacting sliver uniformity and production flow.
To support seamless draw frame operations, LMW provides expert repair and replacement services for critical components, including:
- Differential Gear Box Assemblies – Digital and Analog for LRSB 851
- Scanning Roller Assemblies – Digital and Analog for LRSB 851
- FGearboxes compatible with LDA/1, LDAZ, LDF3, and LDF3 S models
- LRSB 851 Coiler – for smooth material coiling and uniform sliver delivery
Lap Former
For the Lap Former, attention should be given to lap tension control, cleaning of condensers and winding parts, and inspecting the lap drive mechanism. Predictive measures include monitoring lap uniformity through smart sensors and inverter data for speed consistency. Laps may tear or wind unevenly due to misalignment or tension imbalance, leading to breakdowns.
To support seamless Lap Former operations, LMW provides expert repair and replacement services for critical components, including:
- Display - E1061, E1071
- PLC – Microgix PLC, Siemens PLC
- Invertor – E500 Series, E700 Series
Comber
The Comber plays a pivotal role in eliminating short fibers and neps, making precision maintenance essential for superior yarn quality. Key preventive actions include servicing detaching rollers and nippers, sharpening knives and top combs, and cleaning pneumatic lines and suction points to ensure smooth operation and accurate fiber alignment.
Predictive maintenance involves tracking sliver irregularities and monitoring pneumatic pressure levels to catch early signs of inefficiency. Breakdowns in the Comber often arise in the detaching zone, commonly due to clutch wear or air pressure malfunctions, leading to sliver defects or production stoppages if not addressed promptly.
To support peak comber performance, LMW offers specialized mechanical service solutions, including:
- Differential Gear Boxes for models such as LK54, LK64, LK69, and LK69 S
- Nipper Complete tailored for LK54, LK54Z, LK64, LK69, and LK250
Speed Frame
The Speed Frame is critical in bridging the gap between drawing and ring spinning, and its performance directly affects yarn uniformity and efficiency. To keep it running optimally, routine lubrication of flyer bearings and spindles, roving tension adjustments, and regular inspection of the bobbin rail and traverse system are essential preventive measures.
Predictive maintenance comes into play with systems that monitor spindle speed consistency, track energy consumption, and detect early signs of mechanical imbalance. When left unchecked, issues like spindle misalignment or component fatigue can lead to breakdowns that disrupt production and affect yarn quality.
To support consistent drafting and roving, LMW provides expert repair services for key Speed Frame components, including:
- Differential Gear Boxes for Simplex LFS1660 & LFS1660 V
- Differential Gear Boxes specifically designed for LF1400 & LF1400A frames
Ring Frame
Finally, the Ring Frame demands consistent spindle greasing, traveller and ring cleaning, and inspection of drafting zones and lifting mechanisms. Predictive maintenance is enabled by inverter-based monitoring systems that track spindle speeds, piecing quality, and under winding patterns. Breakdown maintenance usually involves addressing spindle drops, brake failures, or inverter system malfunctions.
To ensure smooth and uninterrupted ring spinning, LMW offers specialized mechanical service support, including:
- Motor Cone Pulley (Top Variator)
- Drive Shaft Assembly (Bottom Variator)
By applying the right mix of preventive, predictive, and reactive practices across all stages—from Blow room to Ring Frame—mills can significantly reduce downtime, enhance machine reliability, and maintain high-quality yarn output.
These machines are engineered with easy-access service zones, intuitive user interfaces, modular construction, and integrated diagnostic systems, making routine maintenance faster and more effective. Features like digital service reminders, predictive alerts, and centralized dashboards further simplify maintenance scheduling and reduce the risk of sudden breakdowns.
Another often overlooked aspect is the use of genuine OEM spare parts. LMW strongly recommends using its original spares to maintain machine compatibility, ensure long-term performance, and protect overall machine health. While cheaper alternatives may offer short-term savings, they often result in secondary damage and quality issues—proving costlier in the long run.
For mills looking to modernize their approach further, LMW’s Spin Connect offers a digital solution. This web-based platform provides real-time visibility into machine performance, stoppage reasons, energy use, and more. It enables data-driven decisions, helping mills identify performance dips early and schedule maintenance before breakdowns occur. The result is improved reliability, better resource planning, and reduced unexpected halts.
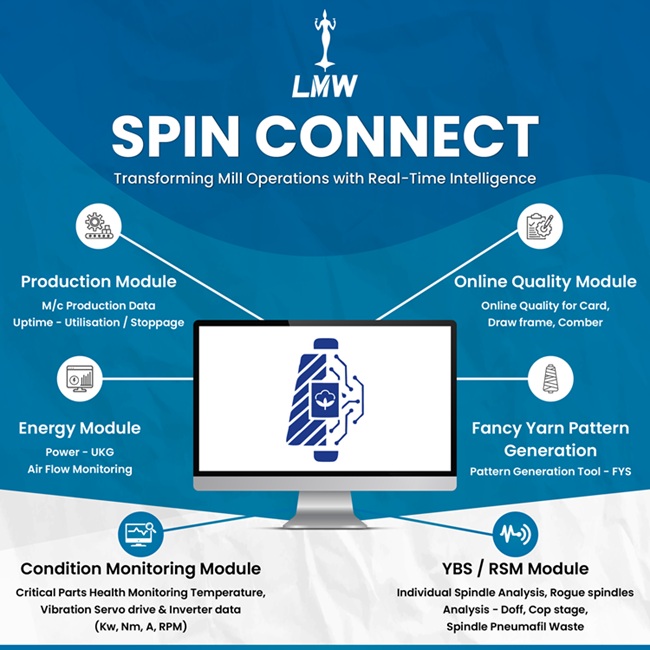
Ultimately, a smart spinning mill doesn’t just invest in machinery—it invests in sustaining it. Maintenance is not a background activity; it's a strategic priority. With the right tools, structured processes, and a proactive mindset, mills can enhance productivity, extend the life of their machinery, and ensure superior yarn quality. Supported by LMW’s advanced machines and maintenance ecosystem, maintenance becomes not just a task—but a competitive advantage.