Blog
Smart Automation in Spinning: How LMW is Engineering the Future
Introduction
In the ever-evolving textile manufacturing landscape, efficiency, quality, and adaptability are more crucial than ever. As mills strive for higher productivity with lower operational costs, automation is no longer optional—it’s essential. At the forefront of this transformation is LMW, driving the shift through its Smart Automation Solutions.
Lets explore how LMW is engineering the future of spinning through Smart Automation.
Smart Automation Solutions
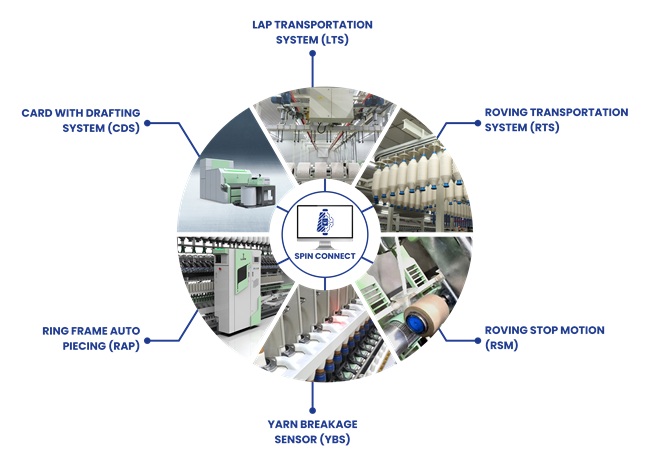
Empowering Spinning Mills through Smart Automation Solutions
As global competitiveness grows, LMW is helping mills shift from manual dependence to Smart Automation solutions built on Digitization, Automation, and Sustainability across Smart Spinning Machinery.
Card with Drafting System (CDS)
The Card with Drafting System (CDS) is designed to enhance efficiency and simplify the yarn preparation process, especially for Spinning, Open-end Spinning and Airjet. It operates at a maximum speed of up to 700 m/min and features a 2/2 drafting system with advanced servo control.
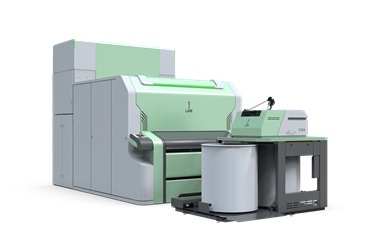
The system includes pneumatic loading of top rollers for easy adjustment, along with auto levelling of sliver through servo drive control. Additionally, it is equipped with auto sliver piecing, making it a highly efficient and user-friendly solution for modern spinning mills.
Lap Transportation System (LTS)
The Lap Transportation System (LTS) is a fully automated solution that ensures the smooth and efficient transportation of laps and spools between the Lap Former and the Comber. It enables accurate positioning and gentle, reliable handling of laps, which helps maintain consistent combing quality. By increasing the operational efficiency of the Comber machine, the LTS contributes to overall productivity improvement.
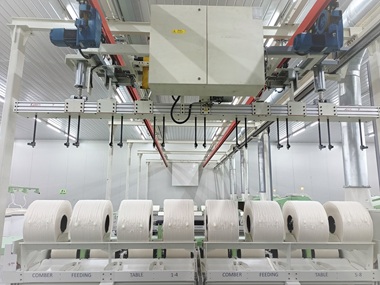
The system features a user-friendly HMI display for easy operation and offers a Lap Turntable option to provide layout flexibility. It eliminates manual errors, reduces operator fatigue, and significantly cuts down on manpower requirements. A single LTS unit can support up to 3 Lap Formers and 18 Combers arranged in a straight line, with a maximum travelling length of 90 meters.
Roving Transportation System (RTS)
The Roving Transportation System (RTS) features a highly reliable and specially designed track made of extruded aluminium with anodized rails, ensuring smooth and efficient bobbin transportation. It is equipped with a motorized drive for train movement and a track motor with brake for precise bobbin transfer and positioning in the Bobbin Stripper or Exchanger. The system includes a bobbin holder with a four-leg design and allows train speed variation through an inverter drive for optimal control.
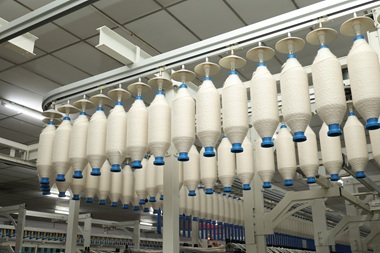
Separate storage areas are provided for full and empty bobbins, ensuring organized handling. The RTS also incorporates an automatic roller clearer and a stripper arrangement for cleaning empty bobbins. Exchanger options are available for both automatic and fully automatic RTS models. With its flexible design, the system can be seamlessly integrated into existing machine layouts, making it a versatile and efficient solution for modern spinning mills.
Roving Stop Motion (RSM)
The Roving Stop Motion (RSM) system is designed to enhance machine protection and minimize waste during spinning. It automatically stops the roving flow during yarn breaks, effectively preventing unnecessary material loss.
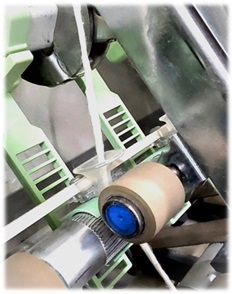
By halting the roving at individual spindles, it significantly reduces pneumafil waste and helps avoid damage to critical components such as cots and aprons. Additionally, RSM contributes to reducing hard waste, making it a valuable feature for improving both efficiency and resource conservation in spinning operations.
Yarn Breakage Sensor (YBS)
The Yarn Breakage Sensor (YBS) is an advanced monitoring system designed to track individual spindles on Ring Frame machines by accounting for traveller rotation. It detects spindle conditions such as breaks, idling, slipping, rogue behaviour, and abnormal slips, displaying them clearly in spot positions for immediate attention.
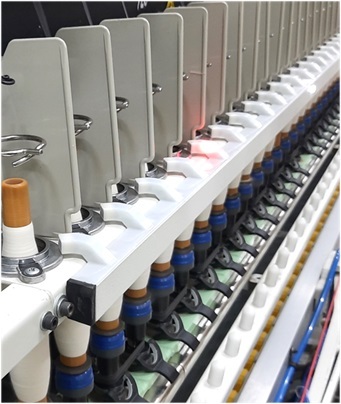
Each spindle is identified with distinct indicators, enabling quick diagnostics. By reducing the need for frequent patrolling, the YBS significantly improves operational efficiency. Additionally, it monitors the breakage rate and enhances piecing efficiency, contributing to consistent yarn quality and improved machine uptime.
Ring Frame Auto Piecer (RAP)
The Ring Frame Auto Piecer (RAP) is a fully automated yarn piecing system that revolutionizes productivity and quality in spinning operations. It works in tandem with the Yarn Break Sensor (YBS) to detect yarn breaks, travel to the affected spindle, and perform the piecing process within just 35 seconds, accurately replicating the "As Human Piecing" (AHP) method.
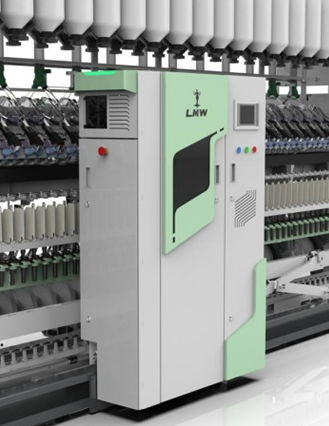
By minimizing manual labor and preventing contamination, RAP not only ensures consistent yarn quality but also significantly reduces manufacturing costs. This state-of-the-art automation can reduce manpower by up to 50% and achieves a high auto piecing rate of up to 60 cycles per hour. With an efficiency greater than 85%, RAP boosts overall productivity while delivering precision and reliability in every piecing action.
Spinconnect
Spin Connect is a web-based monitoring and control system that serves as an all-in-one application, offering a comprehensive view of a spinning mill's performance through a single window. It provides real-time insights into key parameters such as speed, production, stoppages, quality, and power consumption. With smart machine configuration, users can remotely adjust and manage machine settings to ensure optimal efficiency.
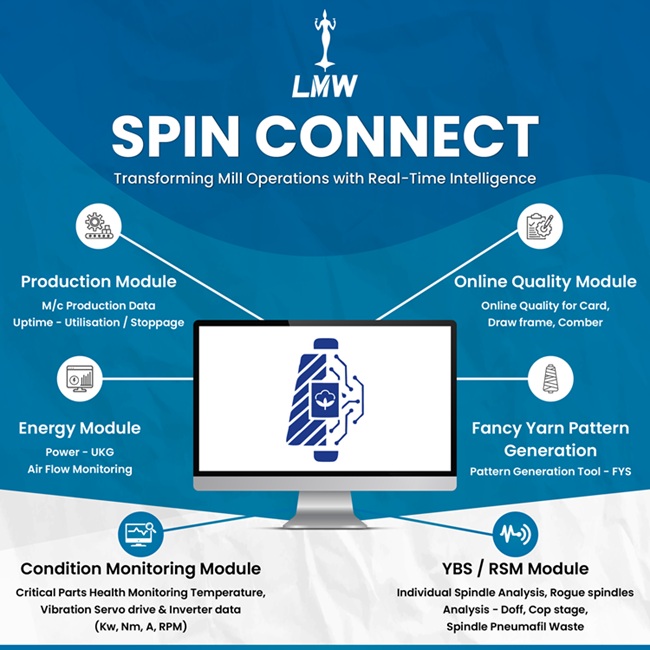
The system also offers remote software support, enabling quick diagnostics and seamless software updates from any location. Operator efficiency is closely monitored, allowing mills to measure and enhance individual performance through real-time data. Additionally, Spin Connect delivers instant mobile and email alerts for any anomalies, ensuring prompt attention and minimal downtime.
Driving Sustainability through Smart Automation Solutions
In an era where sustainability is not just an option but a necessity, LMW is committed to driving environmentally responsible innovations across the globe. With LMW’s Smart Automation Solutions, spinning mills are empowered to minimize resource consumption, reduce hard waste, and lower their carbon footprint — all while improving operational efficiency.
Conclusion
As the textile industry navigates increasing pressure to be more efficient, sustainable, and future-ready, LMW’s Smart Automation Solutions offer a clear path forward. By blending intelligent engineering with deep domain expertise, LMW is not only optimizing spinning performance but also empowering mills to operate with greater environmental and economic responsibility. LMW’s innovations are setting new benchmarks in the spinning world.
The future of spinning is not just faster—it's smarter. And with LMW, it's already here.